In a previous posting, we covered Chapter 8 of
The Toyota Way which deals with Principle #2, "create continuous process flow to bring problems to the surface." Some great comments were posted, and they all focused on the need to have a well-trained workforce when trying to implement flow. I agree. Without an understanding, there's no buy-in for change; without buy-in, there's no chance of success. In that respect, it's of the utmost importance to demonstrate the value of one-piece flow to the individual that it will affect.
However, it doesn't stop there. Eventually, good employees (like the ones in our industry) will adapt to something that's in their own best interest, but they can't always make it happen alone. To switch from a batch system to flow, several isolated
operations must be linked together into one
process. Sometimes, this may be outside the control of associates, team leaders, and supervisors.
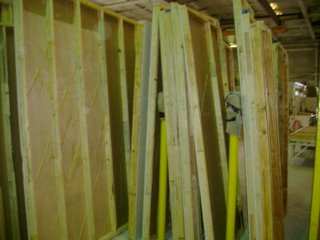
Think about building and setting interior walls. The framers and drywall hangers might work for the wall department, but the wall-setters might work for another department (different team leader, different supervisor, different priorities). At best, the wall department leadership could link the framing and drywall hanging operations into one continuous process flow, but they might have problems integrating with the wall-set operation. That sort of departmental boundary-crossing requires management's involvement, to either change the boundaries or to build consensus between the two departments.
What are some other examples in our processes where managers could create one-piece flow and/or pull systems? Remember, this isn't limited to physical material; it also applies to informational flow.
3 comments:
The effect of Principle 2 is to "bring problems to the surface". This is contray to the traditional mindset which seeks to avoid just that because of fear of being blamed. That's a deeply rooted mindset that will be difficult to overcome.
I agree. Until an organization is comfortable with honestly discussing their issues, one-piece flow will be viewed negatively. It will always expose problems, so it's not ideal for people that strive to hide them.
Everybody: do you feel comfortable putting your errors out in the open?
I would hope that all associates would not have a problem discussing ways to make the production process more efficient and cost effective, even if it includes identifying problem areas or "errors" in their own departments. I think the key to this goes back to "buy in". Does each associate truly believe that lean is a value add proposition? Just as our product has changed and evolved, should not our production process be open to change and evolution as well?
Post a Comment